The elevator industry is a special industry unlike any other within a building with elevators – whether commercial real estate, hospital, retail, hotel, university, residential apartment, and others. It is common for property managers and engineers to feel in the dark about the elevators, escalators, and lifts. The building personnel rely on the elevator service provider for everything about their equipment, and without the data or the knowledge to analyze a situation, they only have 100% of the information coming from the elevator service provider. This is one of the only industries like this, and understanding the trends can be helpful to commercial property managers, real estate investors, engineers, and the like.
What are the latest Elevator Industry Trends?
Recordkeeping
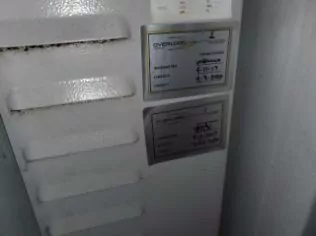
Recordkeeping is a code requirement that is the building’s responsibility; however, the building personnel almost always rely on their elevator service provider for this. The service providers are providing their information stating what they did to the building. Buildings rely on elevator companies and are paying thousands, hundreds of thousands, and even millions of dollars a year without any checks and balances. They rely on the elevator companies. It is interesting that there is governance for all other mechanics and operations of a building, but none for elevator service providers. Buildings can put some governance around elevators by simply keeping their own records – either manually, or with software like the ElevatorApp. The ElevatorApp tracks all of the elevator maintenance service, inspections, testing dates, callbacks, and basically everything you need for your elevators. It has become extremely easy for buildings to keep records (especially since they are required to by code); however, buildings are not doing so.
Passing Inspection
“If I pass inspection, my elevator is fine”. It is common for property managers and others to feel that if they pass inspection, their elevator is working great; This is not always the case. An inspection that’s been completed by the authority having jurisdiction is a safety inspection that was performed to ensure the elevator is code-compliant. An inspection does not take into consideration the performance of an elevator, age, obsolescence, parts availability, callback maintenance, overcharges, and many other variables. Unfortunately, when someone is buying a building, they look at the inspection records and think that because it has passed inspection, the elevator is in great shape – without considering all of the other variables
Proprietary Equipment
The elevator original equipment manufacturers (OEM): Kone, Schindler, TK Elevator, and Otis are installing proprietary equipment – which means that they are the only ones who can provide service on the equipment for numerous years into the future. This is done so that the service providers are locked into a maintenance agreement for years to come, allowing them to charge a premium for their services. Even if the OEM says that the equipment is not proprietary, other service providers will have to spend a significant amount of money for training and tools; Thus, making it difficult for other service providers to maintain the equipment. OEMs are installing their equipment in both new elevator installations and during elevator modernizations, and even offering their products at significant cost savings compared to
others – just to get their equipment in installed. The cost may be cheaper upfront, but the building will usually end up paying more after the installation to maintain the equipment. Machine room-less (MRL) fall under this criterion as well; MRLs are cheaper to install, but the operating cost are astronomical. Developers, architects, and construction companies will typically install MRLs because of the low cost, and the design of the building is usually designed based on only one OEM.
Labor
The construction industry is still booming and installing elevators, but the elevator industry labor pool is shrinking. The number of elevators in the United States is significant (no recent count of existing elevators), and the number of individuals going into the trade is not keeping up with the demand. Retirements are leading to less experienced technicians who are able to work on older equipment; Therefore, there are fewer individuals who can maintain and work on the equipment. Companies are not training technicians on older equipment and the knowledgeable workforce is disappearing. As a result, elevator modernizations, downtime, and callbacks for old equipment needs to be addressed.
A building must stay on top of all the changes in the elevator industry to mitigate any issues. This is difficult for any building, especially when combined with other trends that are taking place: Part availability, obsolescence, in-house mechanics, break/fix maintenance only, remote elevator monitoring, and/or reliability-centered maintenance programs. An elevator consulting firm can help you navigate through industry changes to make sure that your building is protected.